SNG: Synthetic gas for the maritime transition
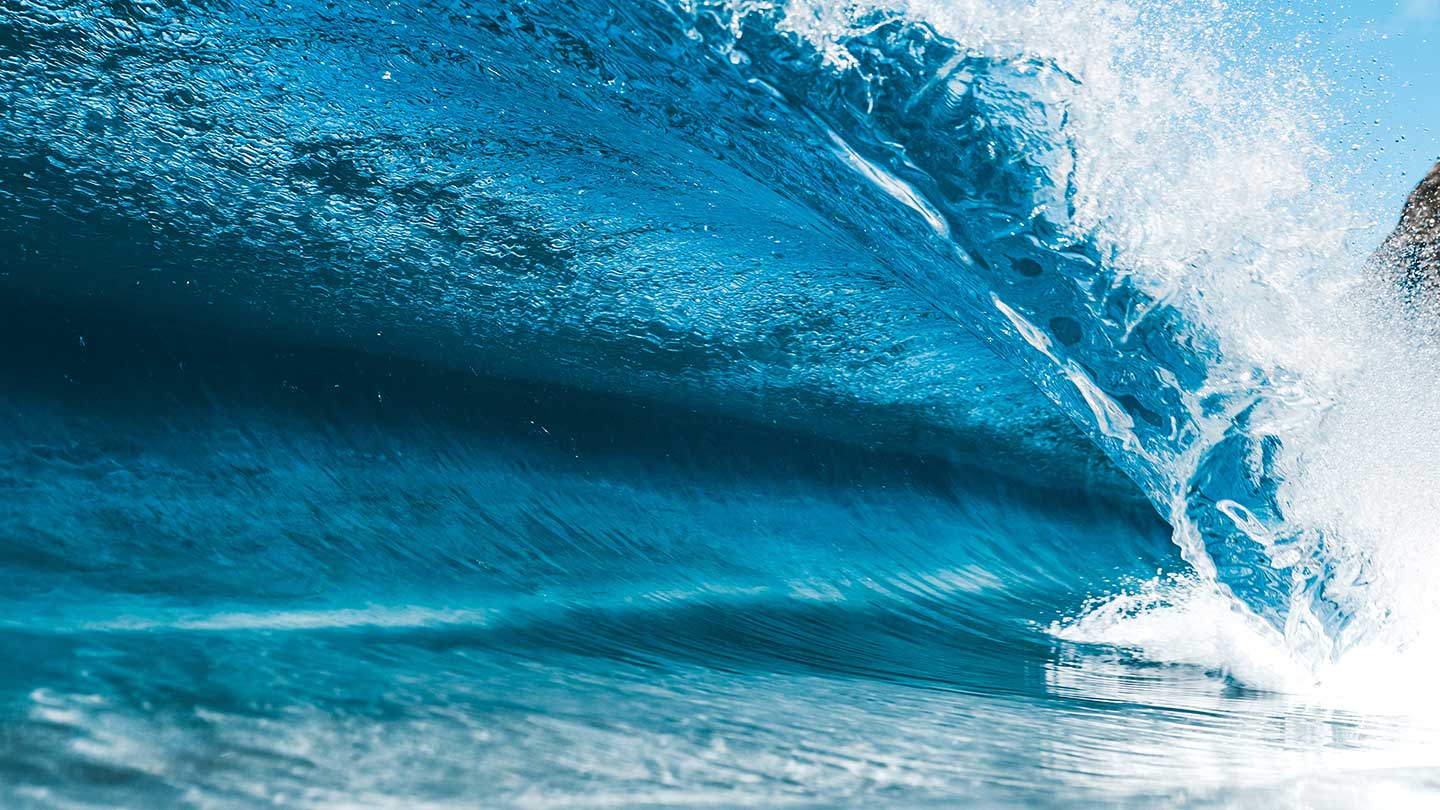
A viable path to decarbonization
MAN Energy Solutions is driving the maritime energy transition with technologies for low-carbon fuels, including green engines and retrofits. Our synthetic natural gas (SNG) solutions offer you a clear path to low-carbon shipping.

From HFO to LNG to SNG
Most of the world's ships run on heavy fuel oil (HFO). The climate crisis has made it essential to find low-carbon alternatives. In recent years, liquefied natural gas (LNG) has become the alternative of choice, but it still a fossil fuel that produces greenhouse gases (GHG). SNG is a new low-carbon alternative. SNG is chemically the same as the main combustible constituent of LNG, so it can used as a direct replacement or blended with LNG, depending on the supply.
SNG as maritime fuel
SNG is optimally suited for the two- and four-stroke dual-fuel engines in MAN’s range and ideal for ships that already run on LNG and aim to save additional emissions. Achieving fuel supply aboard ship is straightforward enough with the right equipment – as with LNG. The new gaseous fuel has to be held at cryogenic temperatures prior to bunkering (-162°C). However, an already established LNG infrastructure can also be used for fueling with SNG.
Reference case: ElbBLUE
World’s first use of SNG in commercial shipping
In September 2021, the 1,036-TEU vessel ElbBLUE, which had been retrofitted with a four-stroke MAN 51/60 dual-fuel engine in 2017, also became the first container ship worldwide to use climate-neutral SNG on a commercial trip. The ship replaced approximately 50% of its bunkered gas fuel with SNG from the Kiwi AG plant in Wertle, Germany. The test proved that any LNG-retrofitted ship can run on carbon-neutral fuels generated by Power-to-X technology.
Read moreManaging Methane Slip
Does the issue of methane slip affect the climate benefits of LNG as an engine fuel for marine applications? Download this paper and find out more about the various countermeasures the company has taken for this purpose.
Synthetic natural gas (SNG) can be derived from fossil fuels and biomass via gasification and methanation processes. SNG can also be produced by, for example, renewable or surplus energy in power-to-gas systems. Biogases are produced from biomass and waste products – and the resulting liquefied fuels can be referred to as BioLNG or LBG (liquefied biogas) and sometimes LBM (liquefied biomethane).
Main advantages:
- SNG and Biogas have the same low NOx, SOx and particulate matter emissions as LNG, but they can be CO2 neutral depending on the feedstock and conversion energy source
- Depending on the source fuel, SNG and Biogas can be a carbon-neutral substitute for fossil fuels
- SNG and Biogas can be blended with LNG to gradually reduce the CO2 footprint
- Considered to be excellent bridging fuels during the ongoing energy transition
Focus areas:
- The availability of SNG and Biogas as bunker fuel
- Increase of production capacities Read more
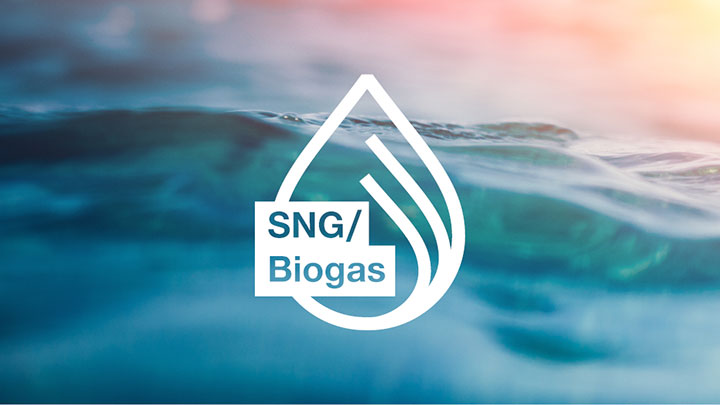
Solutions / technologies by MAN Energy Solutions:
Two-stroke:
|
|
Four-stroke: |
|
Cryogenic equipment |
|
Other future fuels
Related news
MAN Introduces Second-Generation Common-Rail
MAN Energy Solutions has announced a new generation of its Common Rail injection system for its medium-speed, four-stroke portfolio. The CR 2.2 common-rail fuel-injection system will eventually completely replace its CR 1.6 predecessor and builds on its experience, allowing a very precise and flexible control of injection pressure, timing, and duration throughout engines’ entire operating ranges. Engine performance, emissions and fuel consumption can be optimised accordingly.
Stefan Eefting, Senior Vice President and Head of MAN PrimeServ Germany, said: “This new common-rail generation integrates the experience and lessons learned from the previous CR generation. A key development is that we have reduced our dependency on subsuppliers and brought production completely in-house, which – in dispensing with external partners – greatly simplifies the technical side of things for us. The result is a proven, modular system that can easily be adapted to different engine sizes and that I’m positive will be well-received by the market.”
The new CR 2.2 generation is based on the CR 1.6’s extensive field experience running over 17 years on over 500 engines and 5,000 cylinders, representing more than 17,800,000 accumulated operating hours in different applications and fuels. Its core components comprise an optimised and uniform high-pressure pump and a newly developed injector, integrating the CR 1.6 valve group and making the entire system setup more coherent. It is initially being introduced via the MAN 49/60DF engine.
MAN Energy Solutions reports that CR 2.2 can boast of up to 38% increased rail-pressure for all applications, and over 33% increased target time-between-overhaul intervals for most components. The CR 2.2 system features some 35% fewer high-pressure connections, meaning a significantly reduced risk of leakages and greater service-friendliness.
Alexander Knafl, Senior Vice President, Head of Engineering R&D Four-Stroke, MAN Energy Solutions, said: “Common-rail 2.2 brings multiple benefits for engines and engine performance, including reductions in fuel consumption, emissions, vibrations and noise. In general, it offers improved performance and increased robustness compared to its predecessor and has already successfully accumulated over 30,000 engine test hours running on DMA and HFO.”
Other features of common-rail 2.2 include:
- an increased system pressure up to 2,200 bar to comply with future emission limits while offering the best possible fuel consumption;
- an electronically-controlled injector including an accumulator enabling the greatest flexibility with multiple injections and maximum stability during an injection event;
- a reduced modular design for simplified service and allowing the maximum free space for engine maintenance;
- a platform for a broad variety of fuels including HVO and FAME;
- its proven technology with all safety functions from CR 1.6 implemented;
- delivers lower fuel-oil consumption, soot emissions, mechanical load to the engine (due to the reduced pressure-rise gradients in the cylinder), vibration and noise.
MAN Energy Solutions Contacts:
Dr. Johann Wloka, Head of Fuel Systems, Engineering Engines johann.wloka@man-es.com
Robert Strobel, Senior Project Manager - Fuel Systems, R&D Four-Stroke robert.strobel@man-es.com
Documents
-
PR CR New-Gen_EN
Contact
Nils Søholt
Trade Press Marine
Group Communications & MarktingMAN Energy SolutionsTeglholmsgade 412450 Copenhagen SVDenmark
nils.soeholt@man-es.com t +45 33 85 26 69Available languages
- DE ·
- EN